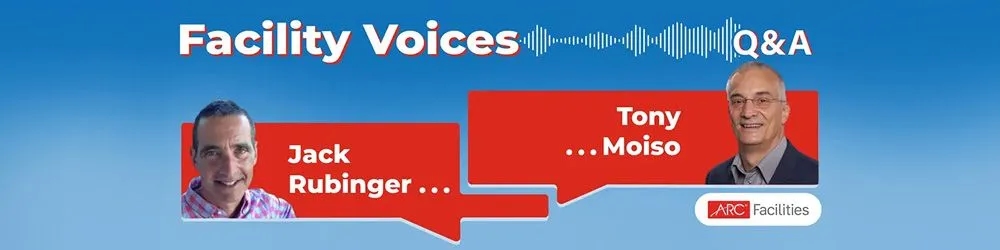
A conversation with Tony Moiso, Director, Facilities Management at Pali Momi Medical Center
Thoughts on reducing operating costs and improving system and equipment reliability and performanceTony Moiso, CHFM, CEM is the Director, of Facilities Management at Pali Momi Medical Center in Hawaii. His skills include process improvement, operations management, healthcare management, and team building.
Tony recently voiced his opinions about using predictive and preventative maintenance in ASHE's Health Facilities Management magazine. Our questions for Tony, below, are based on this article and Tony's experience in the field.
We'd love to hear your feedback on this blog post. Also, if you have topics you'd like to share for Facility Voices, please let us know at solutions@arcfacilities.com.
Jack: What's the best time to implement a Reliability Centered Maintenance program and why?
Tony: RCM is about continuous improvement, so the best time to implement is whenever the organization feels it's ready for that next step. The organization really should have a CMMS and basic preventive maintenance program implemented before applying RCM, though.
Jack: How do you go about creating a robust preventive maintenance system in a hospital setting?
Tony: From a preventive maintenance perspective, hospitals are not different than any other industry. The only real difference is the regulatory requirements, so building in the checks and balances to ensure 100% on-time completion of PMs is critical.
Jack: What are some of the most cost-effective ways of eliminating or reducing system and equipment failure?
Tony: RCM or any other preventive maintenance program are just tools. The most important aspect of any program is the people. Hiring the right staff, training them, empowering them, and building a culture of continuous improvement is the most cost-effective way to eliminate or reduce failures. Bottom-line, people make the difference, not systems.
Jack: How do you reduce operational costs without sacrificing the health and safety of hospital residents?
Tony: A properly implemented and executed RCM program can reduce operating costs and improve system and equipment reliability and performance. RCM can help a facilities maintenance department optimize its resources, both labor & materials, while at the same time reducing failures and improving operational efficiency.
Jack: Compare/contrast preventive maintenance and predictive maintenance. What are the pros/cons of each?
Tony: There are four basic maintenance methodologies; run-to-fail, preventive, predictive (or, condition-based monitoring, CBM), and reliability-centered maintenance (RCM). All four should be applied where appropriate. Deciding which one should be applied is based on regulatory requirements, criticality, results of failure, and whether effective CBM tasks are available. RCM provides the framework for this evaluation.
Jack: How can we use our 5 senses to ensure that hospital patients and staff are receiving a safe, comfortable, and attractive environment?
Tony: The first line of defense for any maintenance program is the front-line staff. Everyone should be continuously monitoring their environment and immediately report any safety, air quality, temperature, or appearance issues. Or, anything they think may be a problem.
Jack: How important is it for your on-the-go technicians to have instant access to O&Ms when they're conducting predictive/preventive maintenance?
Tony: Having access to O&M manuals is critical when developing and implementing the maintenance program, whether it's preventive, predictive, or RCM. Instant access is critical when there's a failure of critical equipment and reducing downtime is of the essence.
Have facilities management software stories you’d like to share with the FM community or want to know more about topics like RCM? We invite you to follow us on Linkedin and share your insights about facilities management best practices.